I. Overview
In recent years, many substations in China have become accidents due to lightning strikes. Most of them are related to the unacceptable grounding resistance of the grid. The grounding grid plays a role of working grounding and protective grounding. When the grounding resistance is too large: When a ground fault occurs, the neutralization occurs. Increased voltage offset at the point of view may cause the voltages of the healthy phase and the neutral point to be too high, causing the device to be damaged beyond the level required by the insulation. In the case of lightning or lightning strikes, high residual currents are generated due to large currents, causing nearby equipment to be counter-attacked and reducing the protective equipment (overhead transmission lines and substation electrical equipment) of the grounding grid itself. The level of lightning resistance cannot meet the design requirements and damage the equipment.
At the same time, whether the grounding resistance of the grounding system is qualified directly relates to the personal safety of the substation operating personnel and the transformer maintenance personnel; however, due to the corrosive effect of the soil on the grounding device, the grounding device has been corroded with the extension of the running time, which affects the safe operation of the substation. Therefore, it is necessary to strengthen the regular monitoring of the grounding resistance of the grounding network; the grounding resistance measurement of the grounding station during operation is caused by the interference of the system's current into the grounding network and the interference between the test lead wires, which results in a large error in the test results. . In particular, the grounding resistance of large-scale grounding grids is very small (usually less than 0.5Ω). Even subtle interferences can have a great impact on the test results; if the grounding grid resistance tests on the grounding grid are inaccurate, not only the equipment is damaged, but also such things as The unnecessary loss of ground network mistakes, etc., combined with my research on grounding network grounding impedance test methods, is summarized as follows:
Second, grounding resistance test principle and method
When measuring the grounding impedance of the grounding device, the current pole should be arranged as far as possible, usually the distance dcG between the current pole and the edge of the grounding device being tested should be 4 to 5 times the maximum diagonal length D of the tested grounding device (parallel wiring method), In regions where the soil resistivity is uniform, two times or more can be taken (triangular wiring method). The voltage lead length is 0.618 times the length of the current lead (flat wire wiring method) or equal to the current wire (triangle wiring method).
1. Potential drop method
Potential drop test grounding device grounding impedance is arranged according to Figure 1 test circuit, and meet the test circuit layout requirements.
G—tested grounding device; C—current pole; P—potential pole; D—maximum diagonal length of the grounding device under test; dCG—distance between the current pole and the edge of the grounded device under test; and x-potential pole and grounding under test The distance of the device edge; d - the test distance interval;
Current I flowing through the test grounding device G and the current electrode C changes the ground potential. The potential electrode P moves outward from the edge of G in the direction of 30° to 45° with the current loop, every interval d (50m or 100m). Or 200m) Test the potential difference U between P and G once, draw the curve of U and x. The flat point of the curve is the potential zero, and the potential between the curve point is the potential of the grounded device under test increases U, and the grounding impedance of the grounding device is:
Z=Um/I
If it is really difficult for the potential test line and the current line to be laid out at an angle, it may be set up along the same path, but keep as far as possible.
If the potential is difficult to determine the flat point of the curve, it may be affected by the grounding device under test or the current pole C, considering the extension of the current loop; or the underground situation is complex, and other methods are considered for testing and verification.
2. Current-voltage meter three-pole method
a) Straight line method
Current line and potential line in the same direction (same path) anti-set as the straight line method in the three-pole method, schematic diagram 2; dcG meet the test circuit layout requirements, dPG is usually (0.5 ~ 0.6) dcG. Potential P should be The measured grounding device G is moved three times in the direction of the connection with the current pole C. The distance of each movement is about 5% of dcG. When the results of the three tests are within 5%, the error can be within 5%.
Large-scale grounding devices are generally not suitable for straight-line testing. If conditions are limited and must be used, care should be taken to keep the current and potential lines as far away as possible to reduce the effect of mutual inductance on the test results.
G—tested grounding device; C—current pole; P—potential pole; D—maximum diagonal length of tested grounding device
dCG—the distance between the current pole and the edge of the grounded device under test; dPG—the distance between the potential pole and the edge of the grounded device under test;
b) Angle method
As long as the conditions permit, the test of the grounding impedance of large-scale grounding devices adopts the current—the arrangement of the angles of the potential lines. The dcG meets the requirements of the layout of the test circuit, generally 4D~5D, and is as far as possible for the super-large grounding device; the length of dPG is similar to dcG. Ground impedance available formula
(2) Correction formula
θ---the angle between the current line and the potential line;
Z''''--- Grounding impedance test value.
If the soil resistivity is uniform, an isosceles triangle with the same dcG and dpG can be used. At this time, θ is approximately 30°, and dcG=dpG=2D ground correction formula 2.
3, grounding resistance tester method.
Figure 3 shows the method of testing the grounding resistance of the grounding resistance of the grounding resistance tester; the test principle, wiring, and requirements are similar to the three-pole method.
1. The E pole must be short-circuited with P1 when using the three-pole method, but the local network grounding resistance is small and the local network grounding resistance is small (≤ 0.5Ω). In order to improve the measurement accuracy, the instrument and ground network measurement are reduced. The influence of the lead resistance and the contact resistance on the measurement result can be solved by unwinding the EP shorting piece. To reduce the error caused by the contact resistance, a separate lead is required to be connected to the ground network test point.
Note:
1, E - connected to the measured network;
2, P1 - connected to the measured network;
3, P2 - then measure the voltage line (its length to take the current line length of 0.618);
4, C - then measuring the current line (the length of the length of the network to take the diagonal 4 to 5 times);
Third, test notes and significance
The characteristics of the grounding device are mostly closely related to the degree of soil moisture. Therefore, the condition assessment and acceptance test of the grounding device should be carried out as far as possible in the dry season and when the soil is not frozen. It should not be in thunder, rain, snow or after rain and snow. Do it now. Through actual measurement, we provide a reliable basis for our rectification. For the substation grounding network grounding situation, a rectification and optimization scheme is proposed to make the grounding network grounding resistance meet the requirements, thereby effectively preventing the step-induced voltage caused by the equipment insulation damage from causing personal injury or further damage to the equipment. To ensure the safe operation of electrical equipment, to create a safe and reliable working environment for substation workers.
Silicone Racket Dampener
About racket dampener:
Silicone racket dampener is widely used in sports.Such as tennis game,badminton game and so on.Racket dampener is one of essentialtennis equipments,it is can be reduce a lot of vibration and reduced wrist injuries while playing tennis,so it is your wirst protector when you play tennis.
Silicone Silicone racket dampener introduction:
1.Product name:Silicone racket dampener,silicone tennis dampener,silicone badminton dampener,racket vibration dampener,tennis vibration dampener,customied tennis vibration dampener
2.Place of origin:Guangdong China
3.Color:any pantone color
4.Logo:Printing,debossed,embossed
5.MOQ:500pcs.
6.Package:1 pcs/opp,customized design is available.
7.Design:Customized/stock
8.Certification:FDA,LFGB,SGS,ROHS,etc.
9.Usage:Use for sports
10.Silicone racket dampener for reference.
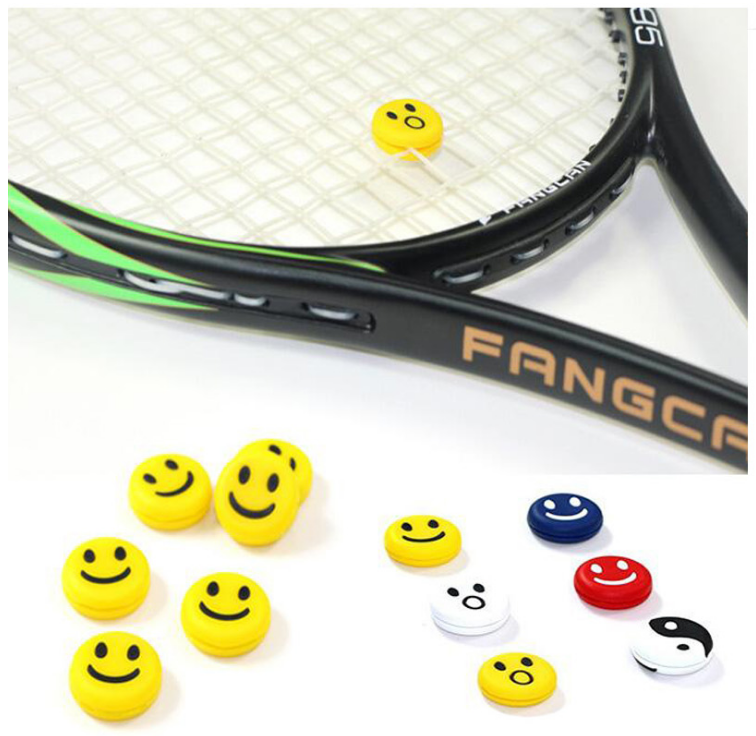
Silicone Racket Dampener,Silicone Tennis Dampener,Silicone Badminton Dampener,Racket Vibration Dampener,Tennis Vibration Dampener,Customied Tennis Vibration Dampener
Dongguan OK Silicone Gift Co., Ltd. , https://www.dgsiliconekitchenware.com