Drone Inspection of a Stack with the Elios 3 UT
The Elios 3 UT was deployed inside the stack, eliminating the need to remove external insulation and delivering precise, repeatable results ideal for routine inspections.
Key Benefits at a Glance
Access Thanks to its compact design, the Elios 3 could navigate the interior of the stack without requiring any external access. This eliminated the need for specialists to dismantle insulation, saving time and reducing risks. |
Safety The team conducted the flight from within a heated area, avoiding the dangers of working at heights or in harsh outdoor conditions. This significantly improved safety and comfort during the operation. |
Adaptability The Elios 3 UT can operate beyond visual line of sight, allowing it to reach areas where traditional methods fall short. This makes it ideal for complex and hard-to-reach structures. |
Reporting The data collected was clear and detailed, providing valuable insights into the stack's condition. This information is essential for maintenance planning and record-keeping. |
Industrial stacks require regular inspections to ensure they remain safe and functional. Visual inspections are typically performed several times a year, while more comprehensive structural assessments are done every 3 to 5 years. These checks help identify potential issues early and support proactive maintenance strategies.
When a visual inspection reveals signs of damage—like corrosion or cracks—a more detailed analysis is needed. That’s where ultrasonic testing (UT) comes in. Using ultrasonic thickness measurement (UTM), engineers can assess the condition of the stack and compare it to historical data and industry standards. Accurate UT results help determine whether the asset is still safe to operate or if repairs are urgently required.
Why a Service Provider Chose a UT Drone Inspection
Osprey Integrity provides UAV-based inspection services that reduce risk and lower costs for clients like BC Hydro, Suncor, and Canadian Natural Resources. In 2023, they were tasked with inspecting an industrial stack at a CNRL facility in Northern Alberta. The stack was part of a once-through steam generator (OTSG), which produces superheated steam by heating water through internal tubes. It also serves as an exhaust for waste gases, reaching temperatures of up to 180°C (350°F).
Because these stacks are insulated, Osprey Integrity uses the Elios 2 or Elios 3 to conduct internal visual inspections. These inspections can detect early signs of degradation, such as corrosion or condensation, that might not be visible from the outside. When these signs indicate a potential risk, UT measurements are necessary to quantify the extent of the damage.
Traditionally, this would involve removing insulation and sending a certified UT technician up via crane or aerial work platform. However, Osprey wanted to test an alternative approach using the Elios 3 UT drone, which could collect data from inside the stack without the need for physical access or disruption to the insulation.
Thanks to the Elios 3’s camera, it is possible to perform UT inspections beyond the visual line of sight. The Cockpit app allows for manual adjustments of gain and gates, as seen on the screen here.
How the Elios 3 UT Conducted Ultrasonic Testing
The main goal of this project was to demonstrate how a drone-based UT inspection could match or exceed traditional methods. The Elios 3, equipped with its UT payload, flew inside the stack through a small access point above the convection section, eliminating the need for cranes or elevated work platforms.
Once inside, the pilot navigated to the targeted area and began taking measurements. The Elios 3’s durable design allowed it to make contact with the inner walls, ensuring accurate readings. It took four measurements in different directions, completing each in under 15 seconds thanks to its advanced system design and couplant delivery mechanism.
This prototype UT probe used in the project features a magnetized hood that helps it attach securely to the inside of the stack.
The entire process took less than an hour, compared to the hours typically spent with traditional methods. Plus, there was no need to disturb the external insulation, making the operation both faster and less disruptive.
What Makes the Elios 3 UT Payload Stand Out?
Osprey Integrity identified several key advantages of using the Elios 3 UT for ultrasonic testing:
- Repeatability: The Elios 3 creates a point cloud of measurement locations, allowing for easy future re-inspections. This enables long-term monitoring of corrosion rates and better maintenance planning.
- Real-time Viewing and Recording: Pilots can see the A-scan in real time and even adjust measurements mid-flight. This reduces the chance of errors and avoids the need for repeated visits to the site.
- Enhanced Access: The Elios 3 can reach spaces that other UT systems cannot, making it ideal for confined or difficult-to-access environments. Its ability to capture LiDAR and visual data simultaneously expands its usefulness.
- Flexible Design: The UT probe can be adjusted to fit different measurement points, and the drone’s laser pointer ensures precise positioning. Pilots can also fine-tune the settings in-flight, ensuring accurate data collection.
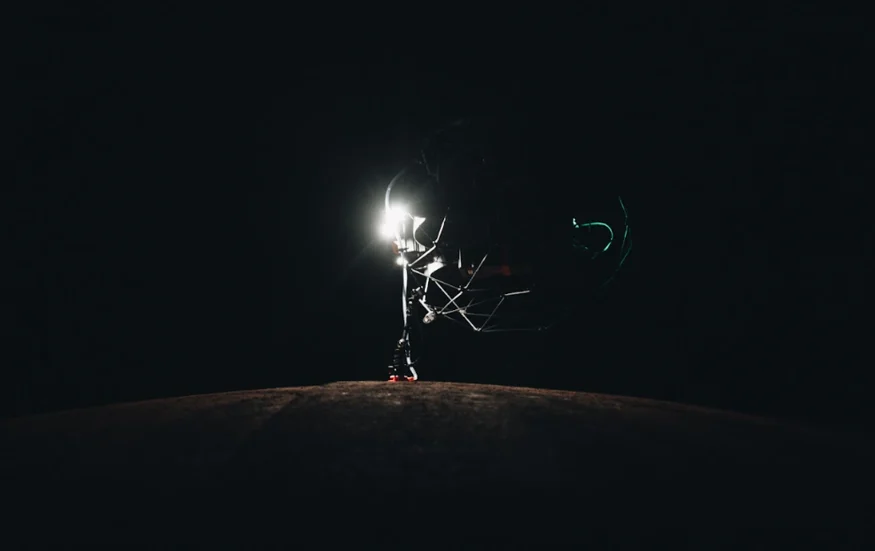
Discover More About the Elios 3 UT Payload
The Elios 3 UT payload was launched in March 2024, with deliveries expected later in the year. It offers a powerful, efficient solution for ultrasonic testing, improving safety, cutting costs, and maintaining high data accuracy. As one of the first companies to use it, Osprey Integrity has already seen significant benefits.
At Flyability’s User Conference in March 2024, Osprey shared their positive experience with the Elios 3 UT during its testing phase. Their confidence in the technology highlights its potential across multiple industries. With its unique capabilities, the Elios 3 UT is setting a new standard for non-destructive testing.
Learn more about the Elios 3 UT payload today.
Zirconium oxide ceramic, also known as zirconia ceramic, is a high-performance material that offers exceptional hardness, strength, and wear resistance. It is made from zirconium dioxide (ZrO2), a highly refractory material that is extremely resistant to heat and corrosion. Zirconia ceramic parts are widely used in a variety of industrial applications, including aerospace, automotive, medical, and electronics.
Zirconia Ceramic,Zirconia Ceramic Plunger,Zirconia Ceramic Ring,Zirconia Ceramic Pipe
Yixing Xiangyang Jiujiu Chinaware Industry Co., Ltd. , https://www.xyjjceramic.com